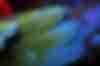
1 The oligomer issue
Polyester production can develop up to 2% of oligomers, and oligomers' formation increases when recycled PET is produced, causing problems during the dyeing process.
During the dyeing process, oligomers migrate to the fibre surface and fibre into the dyebath, resulting in oligomers filtered on the goods and precipitated in the machinery.
Oligomers’ precipitation increases with heat-setting, high dyeing temperatures, long dyeing time, short liquor ratio, high density of packages, and the presence of carriers’ agent.
On the other hand, it decreases by using a suitable oligomer dispersing agent, with short dyeing time, high temperature draining of the dyeing bath, alkaline reduction clearing, alkaline dyeing, and lubricating the fibre after dyeing.
The problems caused by oligomer precipitation are many:
- Undyed dusty deposits on the pes-substrate
- Bad spinning performance
- Reduction of surface smoothness of the fibres
- Development of dust during rewinding
- Deposits in dyeing machines
- Frequent production stops for cleaning
2 Tackling the issue
Our solution to the oligomers problem is PERMULSIN AO 300: the anti-oligomer agent dispersing/sequestering properties for the PES dyeing process.
Permulsin AO 300 has a good anti-aggregation effect, prevents redeposition and filtration of oligomers, and effectively disperses agents for the dyestuff.
It can also be used after the dyeing process as an alkaline PES reduction clearing agent and for machine cleaning, with caustic soda and a reduction agent (in different quantities, depending on the purpose).
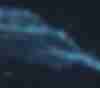