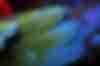
We evolved the competencies and the technical equipment of our in-house fibre applicative lab to the point of supporting our customers along the entire process.
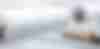
1 Applicative and analytical capabilities
We can analyze every type of fibre, cellulosic or synthetic, and we have analytical capabilities on filament, staple fibres, and nonwoven.
On the filament, we can test and evaluate the oil pick-up, elongation and tenacity, coefficient of friction (F/M, F/F, F/C), and the antistatic properties.
On the staple fibre, we provide analysis of oil pick-up, single filament elongation and tenacity, coefficient of friction (F/M, F/F), antistatic properties, cohesion, carding ability, and bandwidth evaluation.
On nonwoven, we carry out tests to monitor oil pick-up, hydrophilic, hydrophobic, and antistatic properties.
In our viscose pilot plant, we evaluate the various pulp grades, and we carry out filtration tests and spinning trials for standard viscose and modal.
In addition to these, we can perform other chemical analyses such as thermal stability, surface tension, foam test, chemical products identification, PU disk compatibility, corrosion test, and smoke test.
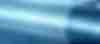
2 Continuous filament
On continuous filament, we perform yarn analysis:
- Oil pick-up (OPU) quantification by Soxhlet extraction with various solvents
- Dynamometric traction test
- Frictional test: coefficient of fiber/metal, fiber/ceramic and fiber/fiber friction (up to 600 dtex)
- Antistatic performance: dynamic charge evaluation
- Abrasive properties of yarn
- Cross-section analysis
In our yarn application trials, we can evaluate the performances of spin finishes and coning oils.
Starting from a "zero-finish" bobbin (OPU < 0,2%, zero-oil yarns, max. 400 dtex / 360 den), we apply the oils at the desired OPU with Fourne device (metering pump, high-speed godets, winder).
We then analyze the yarn characteristics to assess the performance of the spin finish / coning oil by issuing the following parameters: OPU, elongation/tenacity, Friction: F/M, F/C, F/F, and antistatic: Dynamic charge.
The friction test
The yarn is pulled over a friction body at a certain speed and angle. The tensile force is measured before and behind this friction body from this value can be calculated.
The yarn coefficient of friction evaluates the lubrication performance of a spin finish (or coning oil): lower values mean better lubrication.
Using different friction bodies, the Fiber to Metal (F/M), Fiber to Ceramic
(F/C) and Fiber to Fiber (F/F) friction coefficients can be measured.
During the same analysis, we also measure the yarn's dynamic charge, which is directly related to the antistatic performance of the spin finish/ coning oil. Lower Voltage means better antistatic protection.
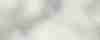
3 Staple fibre
On staple fibre, we perform fibre analysis:
- OPU quantification by Soxhlet extraction with various solvents
- The linear density of single fibres
- Dynamometric traction test of single fibres.
- Antistatic performance: static charge evaluation with Ohm-meter
- Open-end spinning simulation: evaluation of fiber-metal and fibre-fibre friction
- Cohesion and adhesive strength evaluation
- Carding machine: carding-ability and bandwidth evaluation
- Resilience test of fibre for fiber-fill application.
- Wet abrasion number evaluation (WAN)
Our staple application trials can evaluate the performances and comparisons of spin finishes and avivage on a lab scale.
Starting from Zero-finish Staple fibres, we apply finish by spray or immersion bath; the staple fibre passes through the carding machine, and we analyze various fibre parameters: OPU, Bandwidth, Elongation / Tenacity, Friction: F/M, F/F, static charge, cohesion, and adhesive strength.
The Rotoring test
To evaluate the spin finish (or avivage) performance is essential to
assess the lubrication and cohesion of the staple fibres.
With the Rotoring device, we can simulate an Open-End process, measuring the opening force needed to parallelize the
staple fibres.
The fiber/metal (F/M) and fiber/fiber (F/F) friction coefficients can be obtained from the opening force, measured by the Rotoring device, and correspond to the lubrication performance of the spin finish.
During the same analysis, the bandwidth of the fibre sleeve is also measured, giving a direct indication of the cohesion properties of the spin finish.

4 Nonwoven
On nonwoven, we can perform:
- OPU quantification: Soxhlet extraction with various solvents
- Liquid strike through time / repeated strike through test with Lister device
- Antistatic performance: static charge evaluation with Ohm-meter
- Hydrophobicity and hydrophilicity evaluation
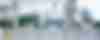
5 Viscose pilot plant
Our state-of-the-art pilot plant can be adapted to produce any viscose fibers, ranging from standard grade to semi-modal, modal, and tyre cord.
New fibre development
Based on your starting raw material and process limitations, we can study the process conditions and chemical consumption to produce any new viscose grade you may want to develop.
New pulp evaluation
With our equipment and knowledge, we can evaluate for you any new grade of pulp, with concerns to filtration, parameters' optimization, and final fiber performance.
Production process optimization
Based on your actual process conditions and our deep know-how, we can optimize your production process in terms of economics, productivity, and final fibre quality.
We can provide you assistance on:
- pulp (evaluation to assess the reactivity of the pulp with NaOH, of the pulp with carbon disulfide, filterability, and the properties of different pulps and their combination);
- modifiers (Evaluation of compatibility of modifiers with viscose and spin-bath, performance improvement of the fibre with various modifiers, and complete evaluation of fibre parameters);
- spinning bath (assessment of the stability of different additives, improvement in spin-bath stability with the addition of suitable compounds, the surface tension of the spin-bath for optimal wetting of viscose filaments, and foam formation control in spinning baths).
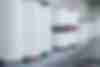